The Challenge
In the quest to mitigate the 13.2 Gt of energy-related CO2 emissions from heating and cooling, our collaboration with TRUMPF aimed to overhaul the conventional heat exchanger design. This initiative sought to address the inefficiencies of existing technologies, leveraging nature-inspired configurations for superior thermal management in an era of escalating global temperatures.
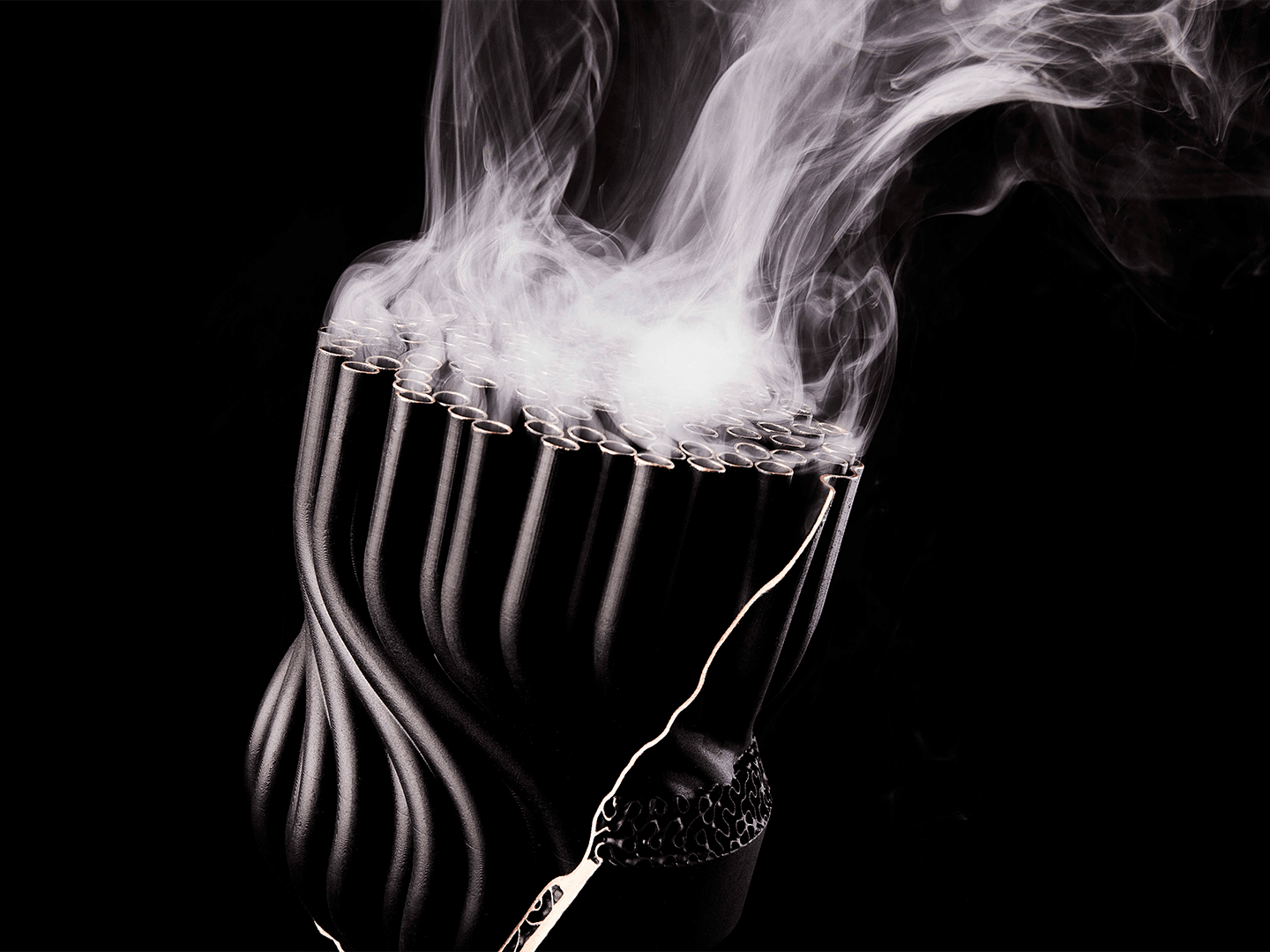
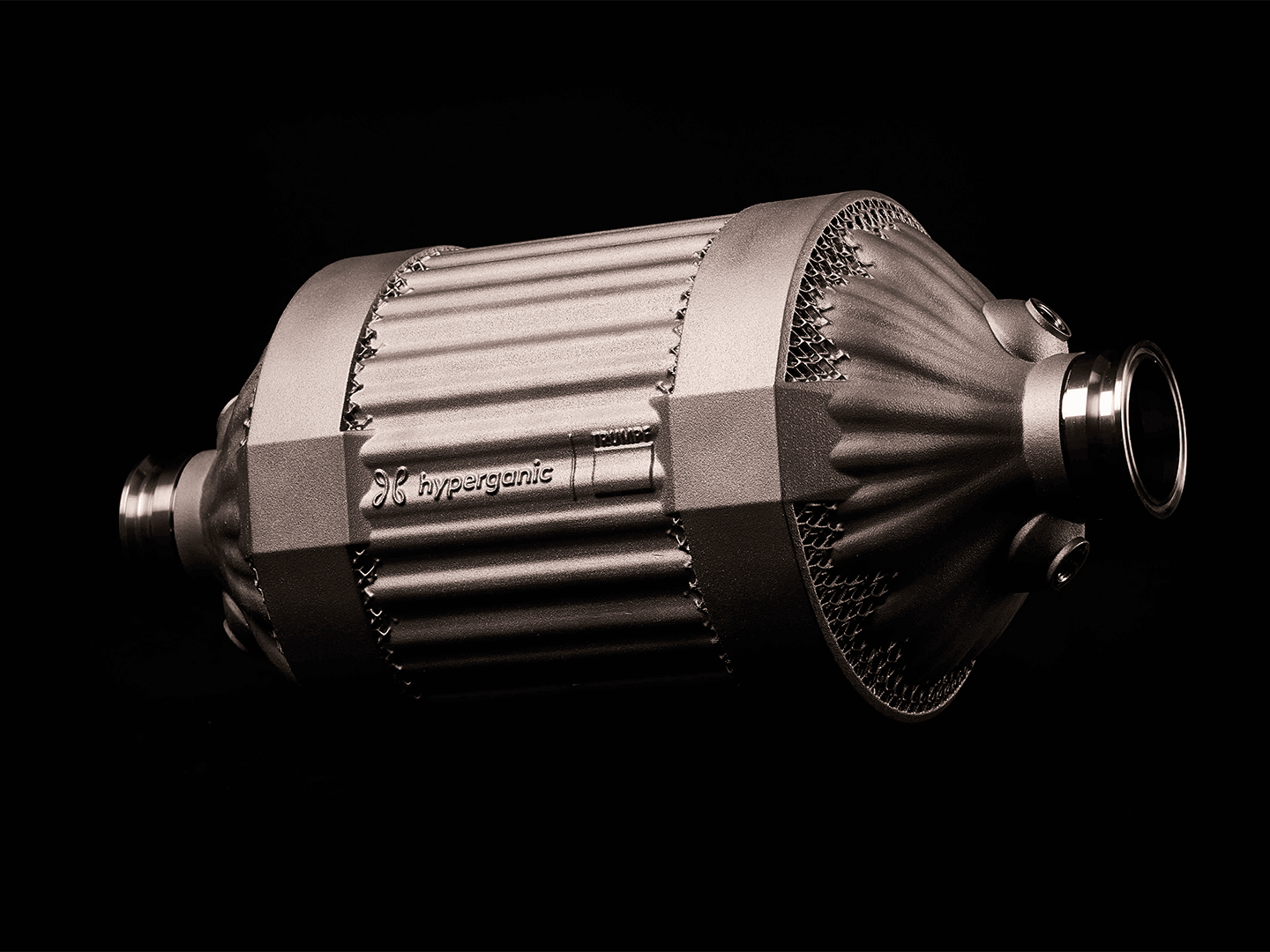